Electronics
6 Reasons Better Manufacturing Cleanliness Leads to Quality Electronics
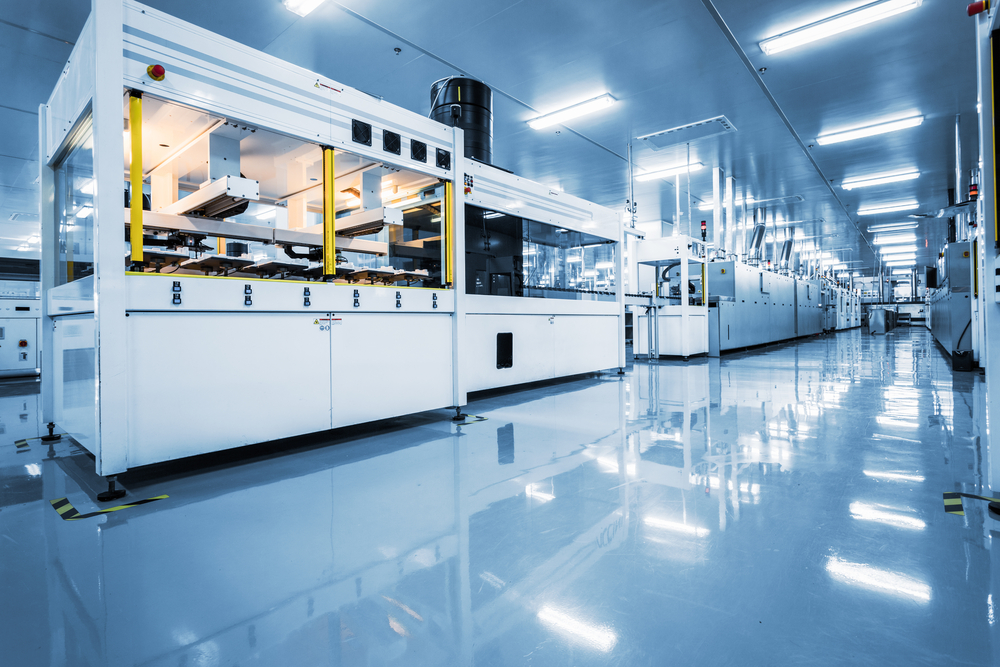
6 Reasons Better Manufacturing Cleanliness Leads to Quality Electronics
Electronics cannot deliver the quality and efficiency that people want without good production hygiene. These are just a few of the reasons why cleanrooms and hygiene practices are critical to the production of high-quality electronics.
Creating hygiene has incredible benefits that are critical to producing quality electronics. Today, there are few mainstream industries in everyday life like electronics manufacturing. Everyone depends on this supply chain for laptops, phones, smart watches, cars and other gadgets. countless more
Without strict production hygiene, these products cannot deliver the quality and performance that people want. These are just a few of the reasons why cleanrooms and hygiene practices are critical to the production of high-quality electronics.
They remove harmful impurities
Imagine opening up a new TV remote to put in the batteries, only to find a strange residue leaking from the electronic components inside. This is not a good user experience and can also pose a serious health risk. Effective electronic manufacturing hygiene prevents such situations from occurring.
First and foremost, the removal of harmful contaminants is the No. 1 reason for improved manufacturing cleaning routines. Different materials are required during the manufacture of different types of electronics, however, the contaminants can vary from one to the other.
Examples of these types of contaminants are adhesive residue, excess solder, and leftover solder paste. Bonding and molding materials, as well as some coatings, can leave behind contaminants without proper cleaning after application.
They improve product life
Most computer professionals today know that cleaning dust from a PC is critical to maintaining top performance. Dust gets into nooks and crannies, blocking airflow and trapping heat where it shouldn’t be, which can age components prematurely.
Proper electronics manufacturing cleanliness has the same positive effect on all the components that go into that PC-like device. Effective cleaning of electronics is key to ensuring they perform at their best for a long time.
This is especially true today. Studies have found that as the gaps between contacts decrease and power densities increase, the risks of electronics failure due to small amounts of contaminant particles increase.
Contaminants are not only bad for consumers. They are bad for PCBs, semiconductors, sensors and all the other electronic components that go into today’s devices. This is especially true in manufacturing. Using clean room preparation helps prevent highly harmful substances from coming into contact with components. This includes things like abrasive fluids that degrade the integrity of the PCB or coating over time, hijacking its product life.
They ensure consistency of quality and performance
Effective electronics manufacturing cleanliness is vital to ensure that electronics are manufactured to consistent quality and performance standards. Quality control is critical to any type of manufacturing. In electronics, however, even small variations in cleanliness can dramatically affect how a component or device performs.
Remember that electronics can go into all kinds of devices, some of which have stability that is mission-critical. For example, air compressor cleaning is critical for PCBs used in robotics development, including competitive robotics and aerospace robotics. Poor quality and performance consistency could lead to robotics competition on Mars due to a glitching NASA rover or a contaminated PCB.
To prevent incidents like this from happening, manufacturers should use clean rooms in electronics manufacturing and treat each component as mission-critical. Using the best cleaning solutions and tools available, as well as a clear cleaning regimen, ensures that every electronic component is flushed out with the best possible quality and performance.
They verify insulation resistance
Heat and thermal management are very important in electronics. Without manufacturing cleanliness, components are already shipped at a disadvantage due to compromised insulation resistance. As mentioned above, any particles that contaminate electronic components can threaten airflow and heat distribution.
By using an electronics manufacturing clean room and thorough cleaning measures, even microscopic particles can be prevented from damaging the integrity of components’ insulation resistance and thermal performance.
These strengthen the durability of electronics
Electronics aren’t designed to be completely fragile – most are made to have protective coatings that help them withstand things like moisture and heat. These features are great for durability, but their effectiveness depends on the integrity of the manufacturing process. If electronics are exposed to contaminants during production, it can lead to weak or ineffective durable coatings.
For example, many coatings are highly dependent on the chemical state of the surface to which they are applied. So if a PCB is exposed to dust, adhesive residue, and solder paste, those substances change the chemical state of the PCB. If the board is regularly cleaned during the production process, these contaminants will be removed and the PCB’s surface chemistry will be restored to normal.
However, if contaminants are allowed to build up on the PCB, protective coatings may not be applied properly, let alone perform as they should. This is a great example of why visual inspection is not effective enough. A PCB may appear clean to the human eye. But that doesn’t mean it’s chemically clean.
In addition, visual inspection cannot tell if the coating is correct. These interactions occur at the microscopic level of chemistry. Manufacturers can’t assume everything is going well without taking all the necessary steps to ensure cleanliness.
They maintain the proper performance of the device.
Finally, electronics manufacturing equipment is worth considering. Electronic components are as clean as the environment in which the component was just assembled Imagine building a computer in a dirty garage on a table full of dust and debris. Regardless of how clean the computer components must be initially. You could also end up with a dirty, dirty computer after mounting it in a place like this. as well as mass production of electronic equipment.
Manufacturing is in a clear trend towards automation. The world demands more and more electronic devices and components.On the one hand, manufacturers must ensure that everyone has access to electronic devices that meet high standards. It also means maintaining a cleaner production environment resulting in better efficiency of production equipment.
This machine has the electronics to do the job. This is because a contaminated environment is harmful to the electronics it produces. Therefore, it is also harmful for the electronic devices that are produced. Therefore if companies pay attention to cleanliness in electronics production. They will see better performance and longer life of their equipment. while delivering products of the highest possible quality.
Robust electronics construction
Electronic manufacturing is all about hygiene. Many factors must be considered by manufacturers during the manufacture of electronic components and devices. A careful cleaning process can slow down the process. To ensure that the best products are produced
Electronics are as durable and efficient as they are. With the right workflow for cleanroom construction and electronics cleaning with just installation. Manufacturers can rest easy knowing they are providing durable, high-performance components that meet today’s computing needs.